Table of Contents
In the world of modern industry, precision and efficiency are key, especially in welding processes. TIG (Tungsten Inert Gas) technology is a solution that has been gaining recognition for years due to its versatility and reliability.
1. Introduction to TIG technology in automation
TIG technology (eng. Tungsten inert gas welding (TIG) is one of the most accurate and versatile welding methods. It is widely used in various industries such as aviation, automotive, medical and chemical industries. Its unique characteristic is the use of a non-consumable tungsten electrode, known for its high temperature resistance, thanks to which the welding process takes place in stable thermal conditions.
The tungsten electrode conducts electricity and creates an electric arc. This arc melts the base material. Thanks to this, it is possible to join elements without using a filler metal. If necessary, a filler metal can be added. A key aspect of TIG technology is the shielding of inert gases such as argon or helium. The shielding gas plays a fundamental role, creating a protective barrier around the electrode and the weld site.
2. Why is TIG key in modern welding?
With the development of automation technology, TIG welding has gained a new dimension thanks to the use of industrial robots. Traditional manual welding, although still present in many plants, is not able to provide the level of repeatability and efficiency offered by robotic systems. Automatic TIG welding allows for the achievement of:
- Consistent weld quality: Thanks to the precision of robots, human errors are minimized, which translates into greater reliability of the final products.
- Increased efficiency: Welding robots can work in continuous mode, which significantly shortens production time.
- Cost optimization: Although the investment in automation may seem expensive, in the long run it brings savings thanks to lower material consumption and reduced losses.
- Work in difficult conditions: TIG technology combined with robotics allows welding in environments that are dangerous or difficult to access for humans.
Thanks to its properties, TIG welding has become an inseparable element of modern industrial automation. An example of such an advanced solution is the OTC NH52-NEFC TIG welding robot cell, which combines the precision of TIG technology with the capabilities of industrial robotics.
In the following sections, we will look at how automation using TIG technology is changing the face of modern industry and what possibilities the presented welding cell offers.
3. TIG industrial robots in modern industry
TIG technology is one of the most commonly used solutions in modern industrial processes, especially where precise welding systems are required. TIG welding automation using industrial robots enables the use of this technology in various industries:
- Aerospace industry: Thanks to precise TIG welding, industrial robots allow the creation of ultra-light and durable structures from aluminum and titanium alloys.
- Food and pharmaceutical industry: In these industries, hygiene and corrosion resistance are the most important. Therefore, welding robots for stainless steel are an excellent choice.
- Energy and chemical industry: Automated TIG welding processes are used to build tanks and pipelines that must withstand extreme working conditions.
Industrial robots such as the OTC NH52-NEFC are ideal for mass production where repeatability and the highest quality are required. Thanks to innovations in welding automation, such systems allow for significant increases in efficiency while reducing costs.
4. TIG welding robot cell OTC NH52-NEFC
The TIG welding robot cell OTC NH52-NEFC is an innovative solution designed to automate welding processes. Designed with the highest precision, it offers efficiency, ergonomics and reliability, which are essential in modern industry.
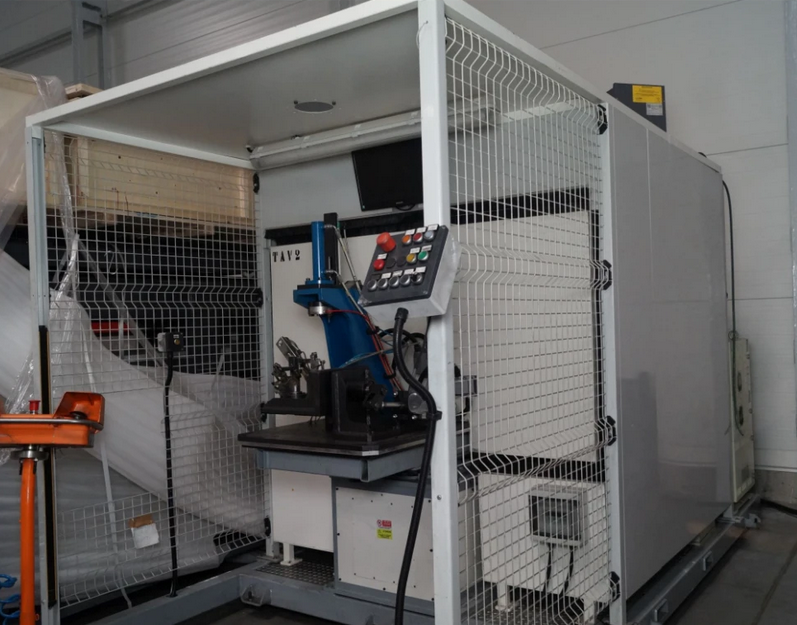
- Country of origin: Italy
- Year of production: 2017
- Station dimensions: 700 x 700 mm
- Shutter width: 1700 mm
- Cell dimensions: 3500 mm x 1900 mm x 2400 mm
Thanks to its compact dimensions, the cell will work well in both large industrial plants and smaller production spaces. Welding robot systems such as this one allow for the simultaneous use of two stations, which significantly increases production efficiency.
The heart of this cell is the OTC NH52-NEFC welding robot, a Japanese technology known for its reliability and precision.
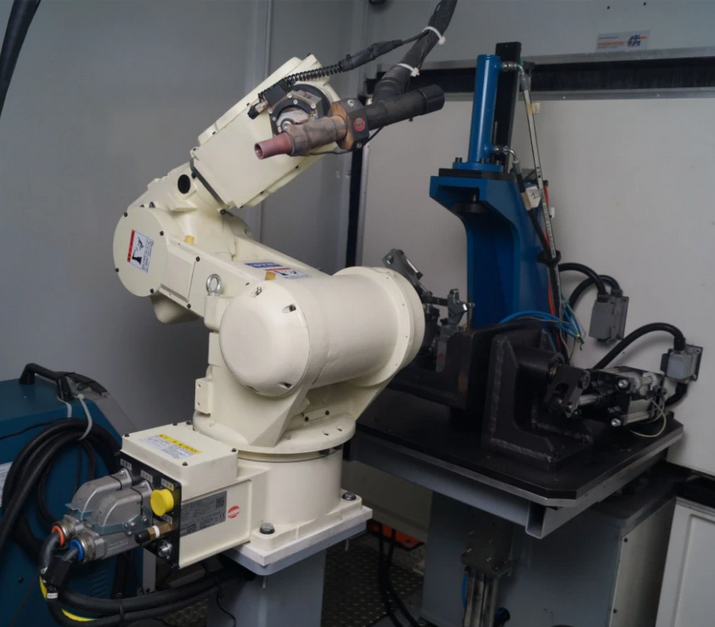
Robot Key Specifications:
- Brand: OTC
- Year of manufacture: 2016
- Number of axes: 6
- Reach: 866 mm
- Payload: 5 kg
- Control: OTC FD 11
- Power source: OTC DA 300-P
The OTC NH52-NEFC robot is designed for precision TIG welding, offering advanced control technology that allows even the most complex operations to be performed. With a reach of 866 mm and a 6-axis design, the robot can reach difficult places. This makes it a versatile tool in industries that require high-quality welds.
TIG industrial welding robots such as the OTC NH52-NEFC offer great flexibility. This means they can be adapted to various tasks. They weld both delicate materials and heavy industrial structures.
The ergonomics of this system allow operators to easily manage the robot's operation, while TIG technology in automation ensures that each step of the process is optimized for efficiency and precision.
5. Conclusion
The OTC NH52-NEFC TIG welding robot cell is a prime example of how TIG welding robots can transform production processes in modern industry. Combining the precision of TIG welding technology with the reliability of automation, systems such as the OTC NH52-NEFC offer many benefits. They enable high-quality welds. They also increase efficiency and help optimize operating costs.
TIG welding technology is distinguished by its exceptional versatility, allowing for the precise joining of a wide range of materials, such as stainless steel, aluminum or titanium. It is this precision and resistance that makes the TIG method so widely used in industry. It is used in the aerospace and aerospace industries, as well as in the food and pharmaceutical sectors. In these areas, hygienic and durable joints are required.