Table of Contents
Modern industry places increasingly higher demands on the precision, efficiency and quality of production processes. OKIO meets these needs by offering advanced solutions in the field of laser welding. In this article, we will introduce you to modern welding technologies that are revolutionizing the way materials are joined.
1. Introduction to laser welding
Definition and working principles of laser welding:
Laser welding is an advanced method of joining materials using a concentrated laser beam. This technology involves directing a high-power laser beam at the joined surfaces, which causes them to quickly melt and fuse. The laser beam is characterized by high precision, which allows for high-quality welds, minimizing the impact of heat on the surrounding materials.
The principles of laser welding are based on several key stages:
- Laser beam generation: Producing an intense beam of laser light using a laser source.
- Directing the beam onto the material: Directing the laser beam onto the joined surfaces using an optical system.
- Melting the material: The energy of the laser beam causes the surface of the materials to quickly melt.
- Weld Formation: The molten materials combine to form a uniform weld upon cooling.
2. History of the development of laser welding technology
Laser welding has its roots in the 1960s, when lasers were first used to join materials. Initially, this technology was used mainly in scientific laboratories, but over time it began to be used in industry.
Key stages in the development of laser welding include:
- 1960s and 1970s: First attempts to use lasers in welding processes. The use of CO2 lasers for welding metals.
- 1980s: Development of Nd laser technology, which allowed for more precise and efficient welding. The first commercial laser welding systems appear.
- 1990s: Application of laser welding in the automotive and aerospace industries. Introduction of robotization of welding processes.
- 21st century: Dynamic development of fiber laser technology, which is characterized by greater power and efficiency. Introduction of advanced automation and quality control systems.
Modern laser welding is an advanced technology that is used in many industries, offering high precision, speed and quality of welds. Thanks to continuous innovation and technological development, laser welding is becoming more and more accessible and effective, revolutionizing production processes around the world.
3. Advantages of using welding technologies
The use of advanced welding technologies brings a number of benefits that translate into improved efficiency and quality of production processes. Here are some key advantages:
1. High precision and welding quality:
- Technologies allow for welds of extremely high quality, which is crucial in industries requiring precise connections, such as the aviation or medical industries. - Precision laser welding minimizes the impact of heat on surrounding materials, which reduces the risk of deformation and damage.
2. Increased production efficiency:
- Automation of welding processes and the use of intelligent quality control systems significantly increases production efficiency.
3. Reduction of operating costs:
- High energy efficiency of fiber lasers and reduced operating costs translate into lower operating costs. - Automation of welding processes reduces the costs associated with manual work and minimizes the risk of human errors.
4. Flexibility and versatility:
- Modular designs of welding robots allow for easy adaptation to various tasks and production requirements. - These solutions can be integrated with existing production systems, which allows for easy adaptation and modernization of production lines.
5. Safety and ergonomics:
- Automated welding systems provide a higher level of occupational safety by eliminating the need to manually perform dangerous welding operations. - Ergonomic designs of robots and automation systems improve working conditions and reduce the risk of injuries.
4. Inter - Plast offer
We are proud to present our product - the Fiber OKIO AB-1410G laser welding robot. This advanced robot is an ideal solution for industries that require the highest precision and efficiency in welding processes
New Fiber OKIO AB-1410G laser welding robot
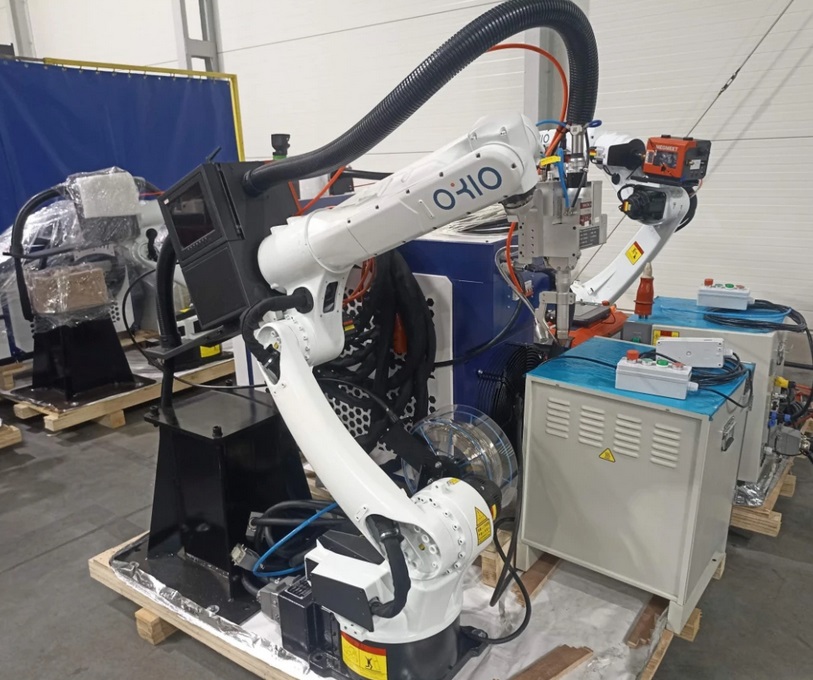
Technical specifications:
- Type: AB-1410G
- Range: 1400 mm
- Load capacity: 10 kg
- Supply voltage: 220V ±10%, 1 phase, 50 Hz
- Laser source: MAX PHOTONICS 3000W
Another robot that is very popular among customers is:
New AB10-1450X laser welding robot
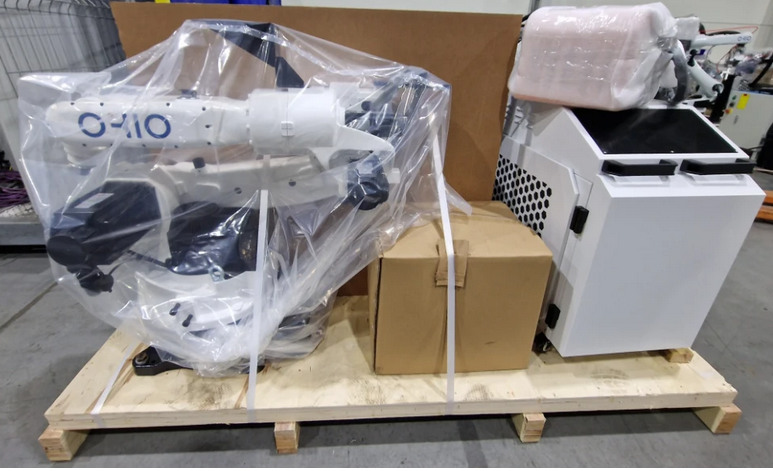
Technical specifications:
- Country of origin: China
- Type: AB10-1450X
- Number of axles: 6
- Range: 1450 mm
- Maximum load capacity: 10 kg
- Laser source: 1.5 kW Max Photonics
- Refrigerator
- Controller
- Remote
- Wire feeder
5. Ending
Inter Plast, thanks to its modern welding solutions and innovations in laser welding, constantly raises standards in the industry. Our metal welding robots, including OKIO industrial robots, provide unrivaled laser welding efficiency. Thanks to automatic welding systems and advanced welding equipment, we offer our customers reliable and efficient solutions. Laser metal welding and laser steel welding with OKIO technology is a guarantee of the highest quality and competitive advantage.